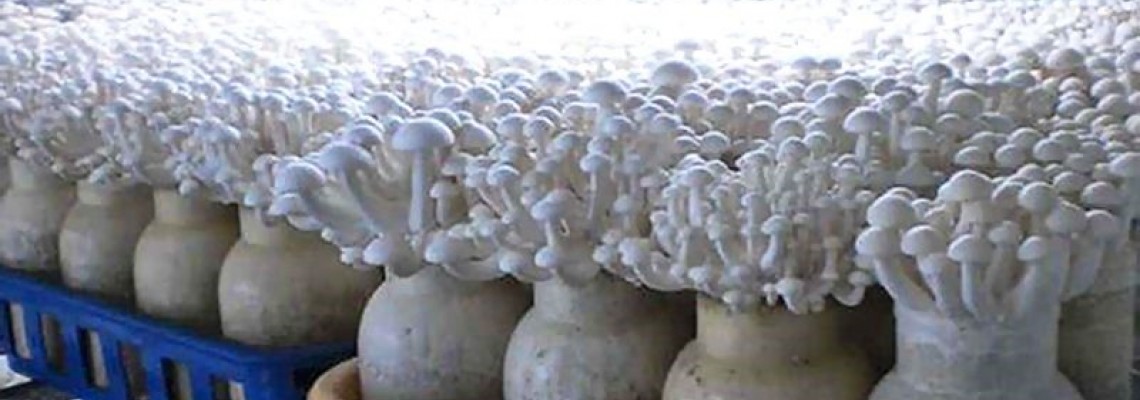
Humidifying print shops and paper mills with fogging systems
The right microclimate in the printing shops is the quality of printing products and the health of the staff. The losses caused by humidity fluctuations are so great that this problem has received increased attention in recent years.
For paper, cardboard and other cellulose-based products, the most suitable conditions are 20-21°C and 50-55% relative humidity.
The absence of a humidity maintenance system leads to instability in air humidification in printing shops. This is often a non-obvious reason for the increase in scrap even in modern and well-equipped enterprises, as a result of which their owners incur significant losses.
There are a number of problems in printing houses with insufficient humidity:
· Paper Dust. Insufficient humidity in the room creates a condition for the rapid drying of the paper and the formation of dust. Paper dust accumulates in ink cans and other surfaces, resulting in unprinted areas and other defects. To fix these problems, you have to stop the printing presses.
· Static electricity. Rolls, reels and bundles of paper during transportation, due to temperature changes, accumulate an electric charge that is difficult to remove indoors with dry air.The resulting electrostatic charges the paper dust. Transferring “stress” throughout the workshop, it disrupts the operation of electronic control units, complicates technological operations, and reduces equipment efficiency.
· Deterioration of paper web quality. Paper comes from factories with an equilibrium moisture content of about 46%. In a room with a dry microclimate, due to the high hygroscopicity of the paper, it immediately starts drying and deformation, the edges are wrapped, flatness is lost. There are regular failures and suspensions of machines, paper waste and ink costs increase. The speed of printing operations is slowing down, the number of rejections is increasing, and the cost of production is increasing.
· Cardboard damage. Cardboard is extremely susceptible to warping and changing its geometric parameters due to the rapid loss of moisture in rooms with dry air. This complicates the accurate and uniform application of images and plates, and complicates subsequent processing of products.
· Deterioration of working conditions for workers. The low moisture content in the air causes the human body to work with increased stress, causing rapid overwork and overstrain. Such a climate reduces the protective functions of the mucous membranes against various infections, and dust provokes redness and pain in the eyes, as well as disruption of the respiratory system.
Together, these problems can significantly complicate the work of any textile production. Therefore, in textile factories, it is recommended to use a high-pressure fogging system.
Installing a fog system in print shops solves important problems:
1. Reducing static electricity. Technological processes and equipment productivity are improving.
2. Reduce twisting and warping. The paper becomes more docile in processing and the process of making adjustments, cutting and packaging of paper products is improved.
3. Improving the quality of folding. Processing and assembly of printed products becomes much easier, which increases the profitability of printing production.
4. Dimensional stability and better color reproduction. In an optimum relative humidity of 50-55% for offset or digital printing, ink adheres much better to all types of paper.
5. Dust suppression. Healthier working conditions and less equipment maintenance.
Air humidification with fogging systems
Injector systems
Leave a Comment