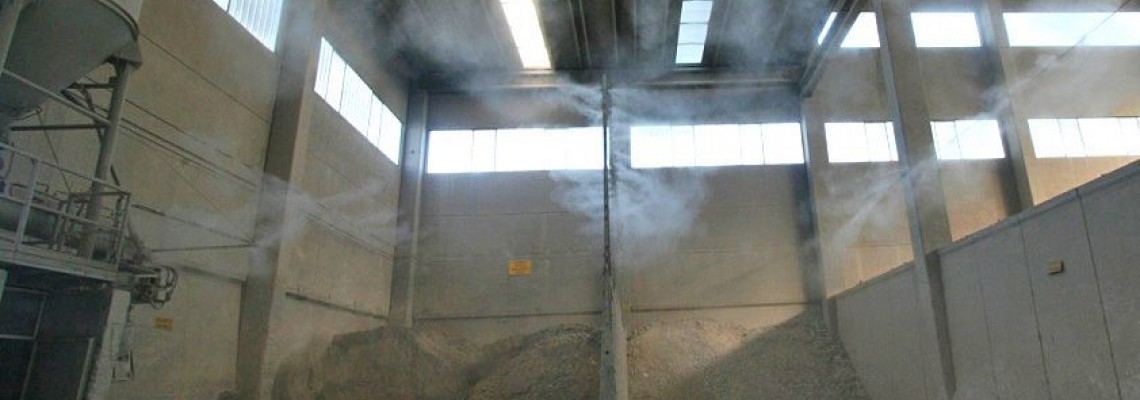
Misting systems for dust suppression in ceramics, glass and building materials
In the production of ceramic products and building materials, a large amount of bulk raw materials is used, which during transportation, unloading and loading is a source of dusting. During the processing and processing of cullet, gypsum and ceramic products, a significant amount of abrasive dust is released into the air.
This leads to a critical general sanitary state of the environment, staff productivity decreases due to the resulting diseases and occupational diseases of workers. Elimination of dust that settles on production equipment, clothing, machinery and units and hovers in the air is simply mandatory, as it leads to damage and breakage of these material assets, which reduces the profitability of production.
In the production of concrete and ceramic products, a large number of different bulk materials are used - concrete, gypsum, clinker, dolomite. And all these materials generate dust during loading, unloading and transportation. Dust pollutes working equipment, machinery, overalls, lighting and heating devices in industrial and warehouse premises.
High pressure misting systems are suitable for dust containment or total suppression. Dust particles "grow" with small drops of water from the fog, become heavier and fall to the floor.
Also, for the normal maturation of concrete products (hydration), it is necessary to maintain high humidity in the steaming chamber. This will retain the water already present in the concrete. High-pressure fogging systems can quickly raise air humidity to 90-100% with little energy. Depending on the size of the chamber and the amount of sprayed water, 1 kg of water will require from 0.01 to 0.004 kWh of electricity to evaporate. And thanks to the droplet size of about 10 microns, the fog jets will not erode concrete products, unlike low-pressure fog systems.
There are two approaches to dust suppression - complete fog coverage of the dust zone with the creation of a wet surface on dusty materials, or the creation of a fog curtain around the dust zone. Which approach to choose depends on the technological restrictions on the moisture content of bulk materials.
The installation of a mist system in the production of building materials solves important problems:
1.Humidified and cooled air - a healthier mucous membrane and stronger immunity for workers, comfortable working conditions due to a decrease in temperature in the workshop where glass is melted, ceramic tiles are baked and gypsum or cement-containing products are thermally dried.
2. Productivity growth - the productivity of the staff increases, the percentage of morbidity caused by harmful working conditions decreases.
3. A healthier working environment – fatigue is reduced, alertness is increased, and the factor of workplace injuries - caused by the concentration of dust in the air - is reduced.
4. Reducing harmful dust - thanks to the dust suppression effect inherent in the operation of the systems, which traps floating dust and substances in the air.
5. Cost-effective solution - when compared to industrial suction systems..
6. Increase profitability - increase revenues by optimizing production processes. Reducing the cost of repairing equipment and its technical preventive maintenance.
High pressure misting systems have a number of advantages:
§Low unit costs of electrical energy;
§Uniform humidification and dust suppression throughout the room;
Leave a Comment